Development of “3D print-thermal spray” systems for applications with dynamic and impact loading - DePriSS
The DePriSS project focused on combining advanced 3D printing and thermal spraying technologies to develop components with improved wear and fatigue resistance under dynamic and cyclic loads. By integrating these two additive manufacturing methods, the project aimed to overcome traditional manufacturing limitations and achieve superior surface properties for high-tech applications.
Within the project duration, several specific achievements were reached:
- Patent Application: A Czech national patent (No. 309502, 2023) was secured for an innovative method enabling direct thermal spraying on 3D-printed components without requiring grit blasting, reducing environmental impact and increasing manufacturing efficiency.
- Industrial Demonstrator: Developed and validated a 3D-printed injection mold core with HVOF-applied surface coatings, showcasing improved cooling efficiency and extended operational life.
- New Material Development: Designed a cobalt-free feedstock powder optimized for dynamic impact resistance, offering sustainable and high-performance alternatives for wear-prone industrial components.
- Collaborative Innovations: Established methodologies for fatigue testing and dynamic impact analysis of coated systems, ensuring the project's outcomes are applicable across multiple industries such as aerospace, energy, and automotive.
- High-Quality Publications: Results were disseminated so far through five peer-reviewed articles and 16 conference presentations, advancing knowledge in the fields of additive manufacturing and surface engineering.
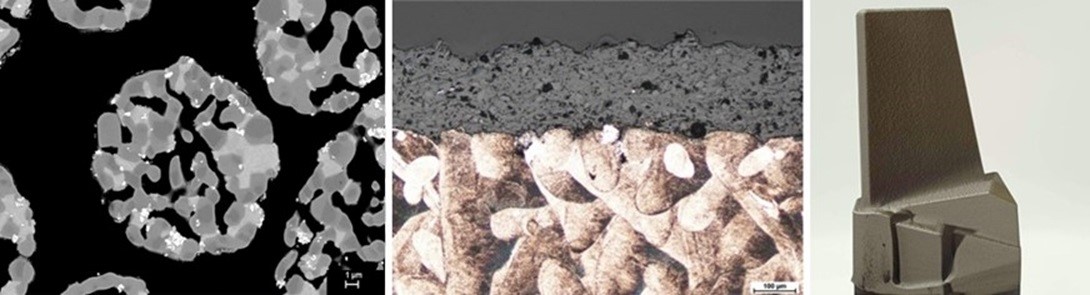