Multi-scale simulation of laser welding for optimal battery pack manufacturing - LaserBATMAN
Project summary
The use and production of batteries in the automotive industry began roughly a decade ago with the purpose and aim to produce highway-capable long range electric vehicles. With the current increased demand in industry to produce more efficient energy sources, the manufacturing of electric components need be of high quality and assure the intended performance. This has not yet been fully addressed from an industrial perspective due to short development times. The project will study and optimize joining processes for different stages of battery manufacturing, from battery cells to battery packs. Laser welding is the preferred method of joining and effects related to e.g. residual stress, heat transfer, defects and resulting electrical resistance will be studied and optimized as well. Simulations of the assembled battery packs will enable industry to optimize for example laser process parameters for the joining processes and thereby maximize the efficiency and quality of production.Project Details
Call
Call 2021
Call Topic
Modelling for materials engineering, processing, properties and durability
Project start
31.05.2022
Project end
30.05.2025
Total project costs
1.234.835 €
Total project funding
937.422 €
TRL
3 - 6
Coordinator
Prof. Kent Salomonsson
kent.salomonsson@his.se
University of Skövde, HOGSKOLEVAGEN 1, 54 128 SKOVDE, Sweden
Partners and Funders Details
Consortium Partner | Country | Funder | |
---|---|---|---|
Resolvent https://www.resolvent.com |
SME | Denmark | DK-IFD |
University of Skövde https://www.his.se |
University | Sweden | SE-VINNOVA |
Technical University of Denmark https://www.dtu.dk |
University | Denmark | DK-IFD |
Volvo Group Trucks Operations https://www.volvogroup.com |
Large industry | Sweden | No Funding |
Aurobay Powertrain Engineering Sweden |
Large industry | Sweden | No Funding |
Keywords
processing-structure-property relationships, multiphysics, multiscale modeling, digital twin, manufacturing processes, Constitutive modeling, Computational simulation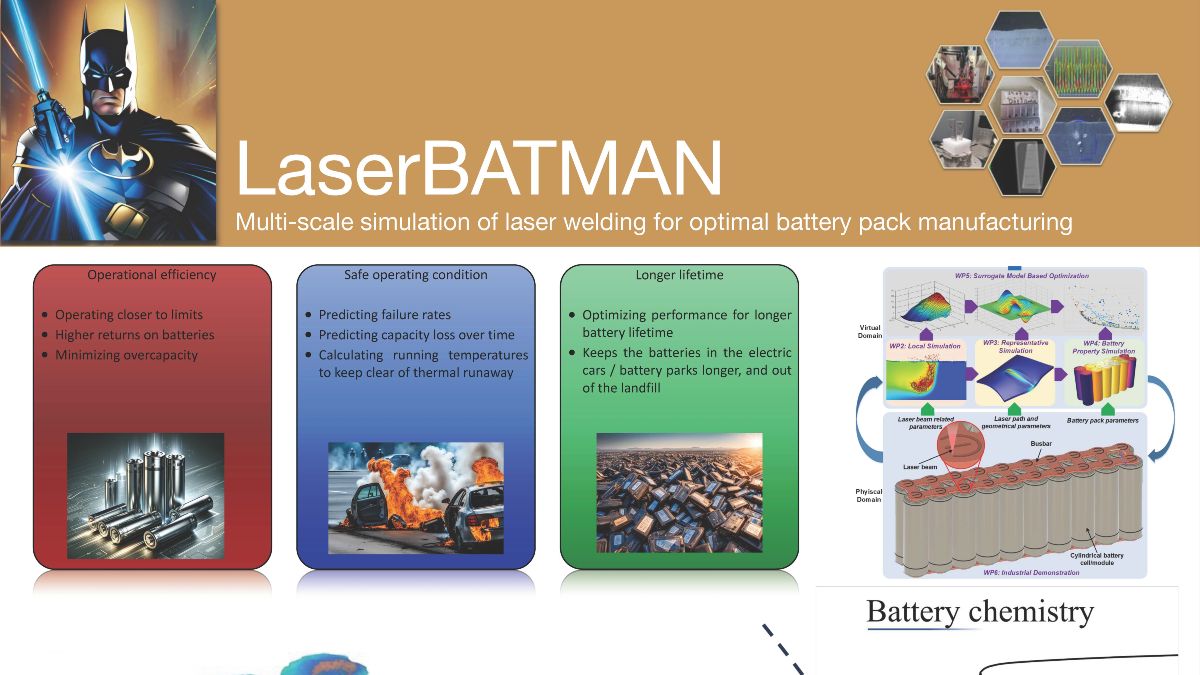